Durable, Efficient Automated Powder Coating
Our dedicated 630-foot automated powder coating line applies durable finishes to your metal parts in-house, streamlining production of your manufactured and marked parts.
Overview of capabilities
Our 630’ long automated powder coat line offers both automated and manual powder application. We also provide pre-treatment with Iron Phosphate (ideal for mild steel) or Zirconium (for aluminum and stainless steel). In addition, we provide in-house screen printing, pad printing, and laser etching to finish parts with required feature marking or part identification.
Benefits of powder coating
Versatility
- Virtually all metals can be powder coated. We partner with trusted sub-tier suppliers for other materials requiring other paint or coating applications.
- Precise control for consistent coverage
Aesthetic Flexibility
- You get what you want, with a wide array of finishes: smooth, matte, gloss, or textured
- Virtually unlimited color options
Durability
- Resistant to chipping, scratching, fading and wear
- Excellent corrosion protection for outdoor and industrial use
Cost-Effective
- Automated line means less lead time and quicker completion
- Long-term savings with fewer touch-ups, repairs and replacements over time
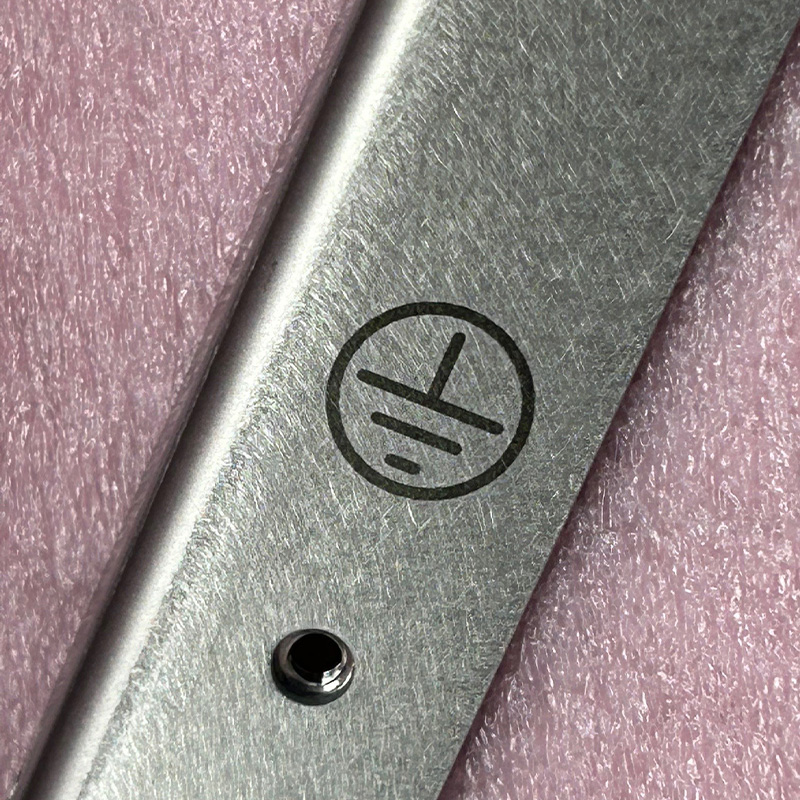
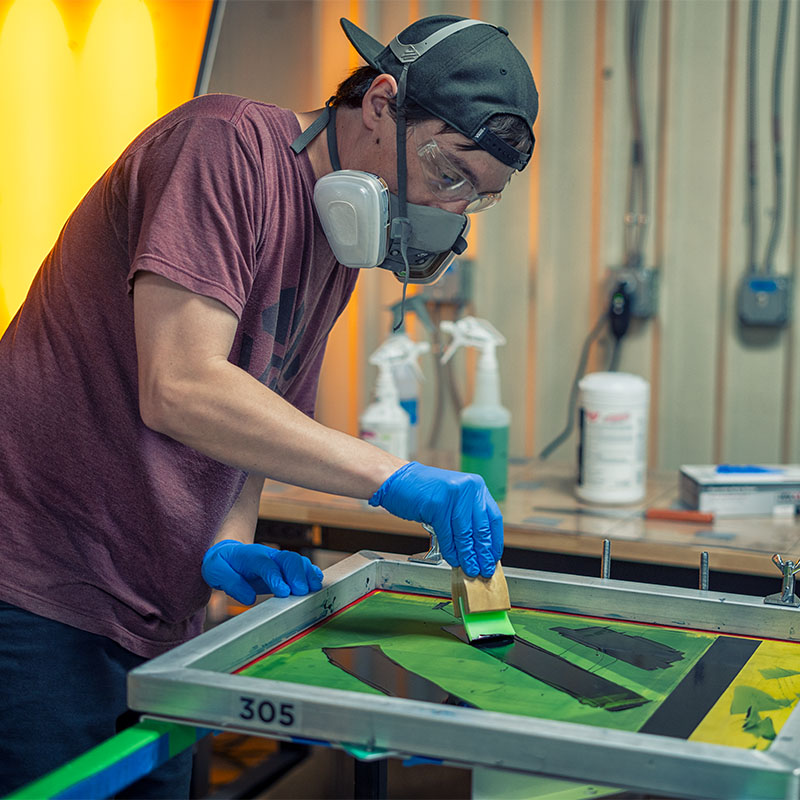
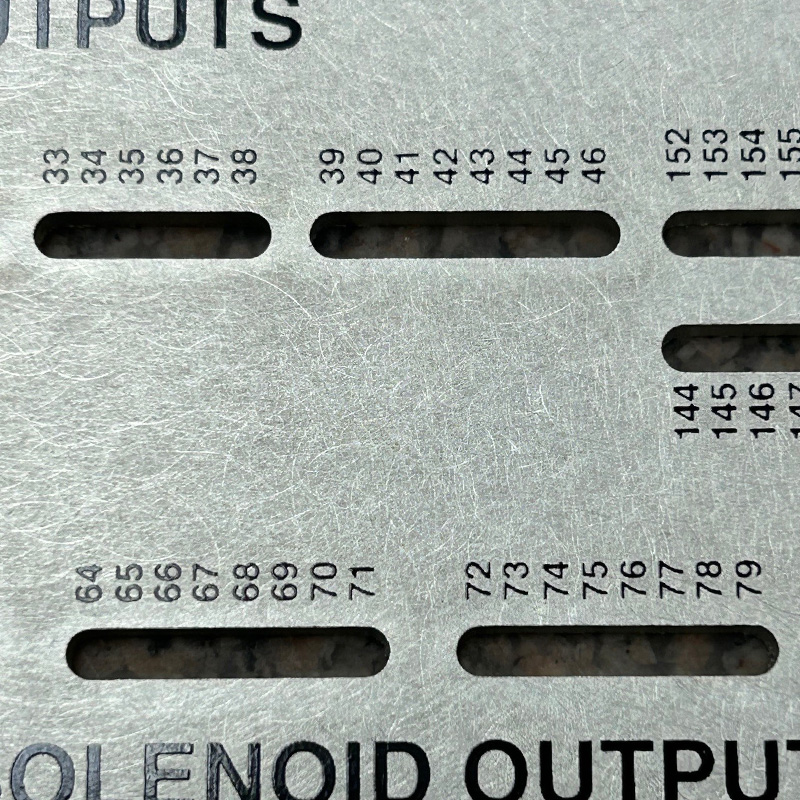
Part Marking
Our in-house part marking services create long-lasting marks on your part surfaces, helping with traceability and identification. With multiple marking solutions, we’re able to handle screen printing, pad printing, laser part marking (both fiber and CO2 lasers), as well as traditional vinyl applications. Our team is ready for whatever your part marking needs may be.
Color and finish options
Your color and finish opportunities are endless with color and finish combinations to meet any of your part needs. If you have a special request, during the quote review process our team will walk you through what we’re able to do for you.
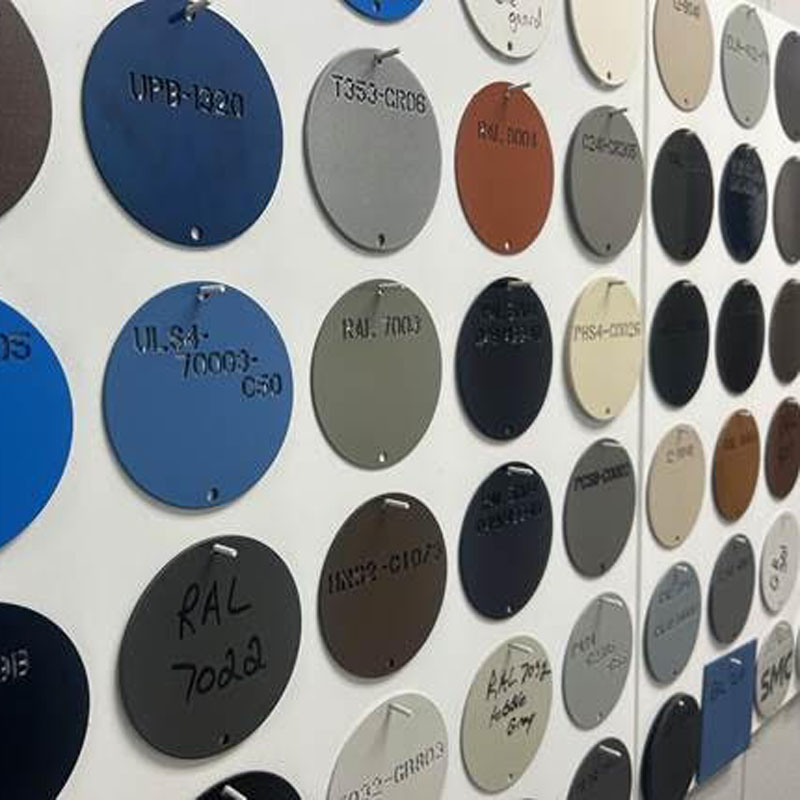
Other coatings / services available
While we handle most manufacturing and coating processes in-house, for other specialized coatings and services listed below, we work with premier sub-tier partners to perform the following processes:
- Anodizing type II & III
- Chromate Conversion/Chem Film
- Electroless Nickel
- Egyptian Coating
- Zinc – clear, gold, black
- Passivation
- Tin Plating
- Clean Room
- Wet Paint
- CARC
- Gold, Silver, Chrome, Platinum Plating
- Electropolishing
- Heat Treat
- Plasite Epoxy
- MMO coatings
- Plastic Welding
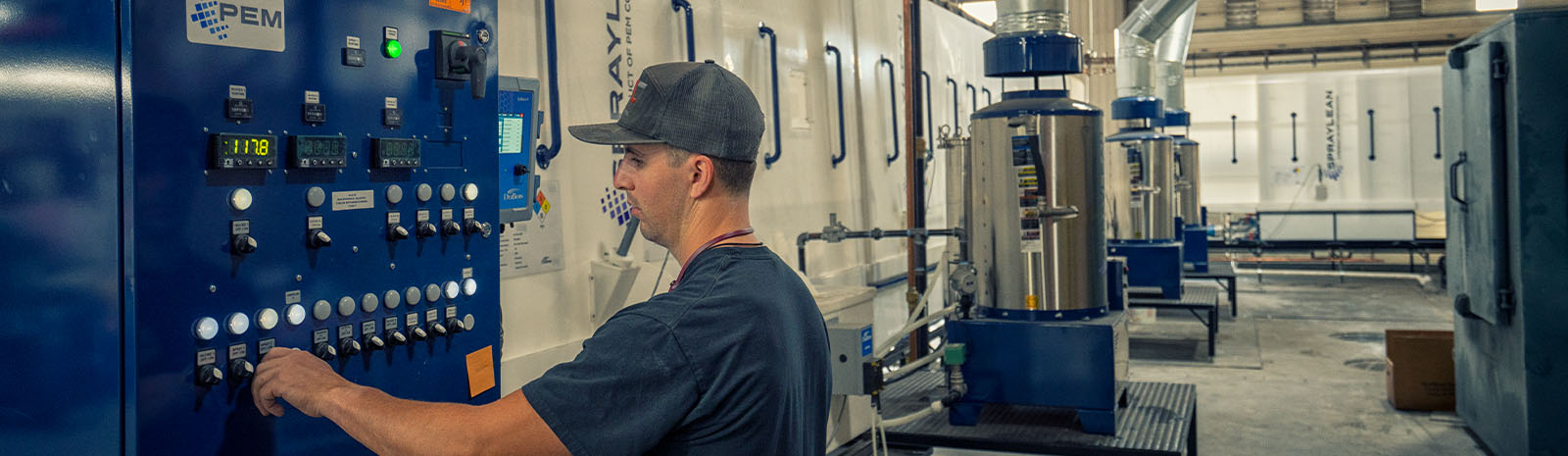